Ersten Hochrechnungen zufolge werden im Jahr 2016 in Deutschland etwa drei Millionen LCD-Bildschirme dem Recycling zugeführt. Diese enthalten jedoch oftmals noch eine quecksilberhaltige Hintergrundbeleuchtung und sind deshalb im Sinne der AVV als „gefährliche Abfälle“ und im Elektro-Gesetz unter der Sammelgruppe 3 einzustufen. Daneben sind wertvolle Rohstoffe wie Metalle oder Kunststoffe darin verarbeitet, die möglichst schonend zurückgewonnen werden sollen. Aus Mangel an geeigneten automatisierten Verfahren konnten die Geräte bisher jedoch nur aufwendig per Hand auseinander genommen werden, was die Gesundheit der Arbeiter gefährdete. Der Recyclingexperte Erdwich Zerkleinerungssysteme GmbH bietet deshalb nun eine Alternative: Das Kauferinger Unternehmen hat ein Verfahren zur automatischen Aufbereitung von LCD-Bildschirmen entwickelt, sodass Quecksilber und wertvolle Rohstoffe einfach entnommen und umweltschonend wiederverwertet werden können.
Flachbildschirme bestehen aus bis zu sieben Schichten. Diese enthalten neben der wertvollen Metallverbindung Indium-Zinn-Oxid (ITO) auch Quecksilber in der Hintergrundbeleuchtung. Laut Gesetzgeber müssen die Geräte deshalb so behandelt werden, dass weder die Natur noch der Mensch durch den giftigen Stoff belastet werden. Da das Umweltbundesamt Verwertungsquoten für Elektroschrott festgelegt hat, dürfen die Bildschirme nicht auf Mülldeponien entsorgt werden. Für Maschinen war die Zerlegung bisher jedoch zu komplex, sodass diese vorerst noch manuell erfolgte.
Besonders die Demontage von LCD-Bildschirmen mit flächiger Hintergrundbeleuchtung war bisher mit einem hohen Zeitaufwand verbunden. „Allein um die Gehäusehälften zu trennen, müssen bis zu 30 Schrauben entfernt werden. Je nach Aufbau des Bildschirmes und Art der Hintergrundbeleuchtung dauert die Zerlegung durch geschultes Personal so zwischen 8 und 20 Minuten“, erklärt Harald Erdwich, Geschäftsführer beim Recyclingexperten.
Aufbereitung in vier Prozessschritten
Als zeitsparende Alternative hat Erdwich eine Anlagentechnik entwickelt, die mittels Kamerasystem und Roboter Bildschirme bis zu 55“ automatisch unter sicheren Bedingungen auffräst und zerlegt. Die Aufbereitung erfolgt in vier Schritten: Zunächst werden die einzelnen Bildschirme auf ein Förderband aufgegeben und in einen geschlossenen Verarbeitungsraum transportiert, wo sie in die Prozessposition geschoben werden.
Ein Roboter mit vier verschiedenen Arretierungsarmen zentriert jedes Gerät und hebt es anschließend in die Endposition für den Bearbeitungsprozess. Hier vermisst ein Gelenkarmroboter die Konturen des Bildschirmglases mittels Kamerasystem. Sobald die Koordinaten berechnet wurden, fräst der Roboter das komplette Gehäuse auf. Dabei anfallende Späne werden automatisch über ein Filtersystem abgesaugt.
Nach jedem Fräsvorgang werden die Werkzeuge automatisch per Kameratechnik überprüft, sodass ein möglicher Bruch rechtzeitig erkannt wird. Außerdem überprüfen die Kameras den Verschleißgrad der Fräser. Bei Bedarf weist das System den Operator darauf hin, die Geräte auszutauschen, damit die Prozesssicherheit weiterhin gewährleistet bleibt. In einem dritten Schritt werden in einer Unterdruckkammer die verschiedenen Schichten wie die mehrlagige Polarisationsfolie sowie die Streuscheibe entnommen.
Durchsatzleistung von bis zu 45 Geräten pro Stunde
Zum Schluss erfolgt die Entfernung der Hintergrundbeleuchtung. „Für die quecksilberhaltigen Gasentladungslampen steht hier direkt in der Kammer ein geschlossener Entsorgungsbehälter bereit“, erläutert Erdwich den Prozessablauf. „Gleichzeitig wird die entstehende Abluft kontrolliert abgesaugt und über eine Quecksilber-Filtertechnik aufgefangen, wo das schädliche Metall in ungiftiges Sulfid umgewandelt wird.“ Zuletzt wird der Bildschirm ausgefördert und kann in einer nachgeschalteten Anlage weiter aufbereitet werden. Das wertvolle Indium-Zinn-Oxid etwa, das in der Leiterplattenproduktion verwendet wird, befindet sich auf zwei dünnen Glasscheiben in Leiterbahnen. Da die Metallverbindung weltweit zunehmend stärker nachgefragt wird und die Preise in den vergangenen Jahren einen rasanten Anstieg verzeichnet haben, lohnt sich eine Wiederverwertung des Rohstoffes besonders.
Neben LCD-Bildschirmen mit bis zu 55“, die mit Hilfe von Robotern in einer automatischen Aufbereitungsanlage zerlegt werden, bietet Erdwich auch ein Monitorsägesystem für LCD-Monitore bis 25“ an. „Konnten vorher per Hand etwa vier bis sieben Geräte demontiert werden, sind nun 60 Bildschirme pro Stunde möglich – und das vollkommen ohne gesundheitliche Risiken“, so der Geschäftsführer.
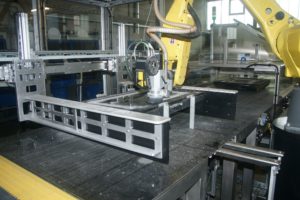
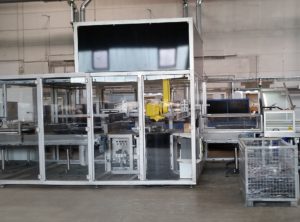
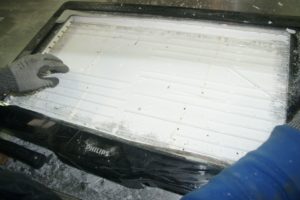
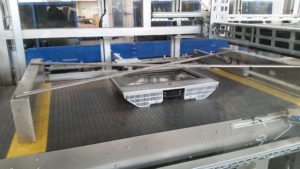
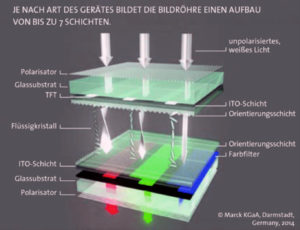
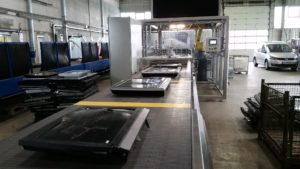